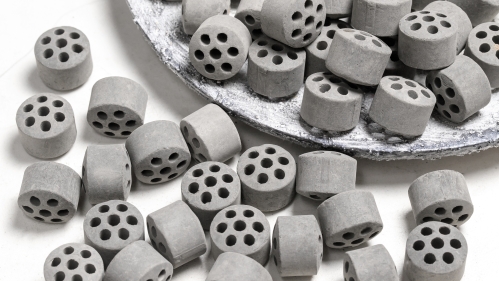
Catalyst Manufacturing Center
Significance of Catalysts
Catalysts are essential components of many industrial processes, ranging from catalytic converters to fuel cells to the production of new pharmaceuticals and the manufacture of materials for solar cells. Worldwide sales of catalysts amount to tens of billions of dollars per year, with about 5% growth rate per year. In addition to their industrial importance, the environmental impact of catalysts is significant. The amount of energy and raw materials needed for manufacturing of chemicals and materials is greatly reduced by using catalysts. Catalytic converters reduce the air pollution from cars to a great extent, and thus are an important environmental engineering application. The manufacturing of materials for innovations in clean energy, medicine and IT cannot be carried out without catalysts; this includes critical materials for solar cells, wind turbines, battery storage, computers, phones, medical devices and medicines.

Design of Supported Catalysts
Supported catalysts involve distribution of the active catalytic material (which is usually a metal) through a porous solid support. Modern supported catalysts have many advantages, such as high surface areas, a low amount of the often expensive active metal component and high mechanical and thermal stability. The design of a typical supported catalyst involves a large number of quality attributes. For a catalyst pellet this may include specified loadings of active metal(s) in the support, a specified distribution of active metal(s) from the center to the surface, and specified dispersion. Optimal catalyst quality allows one to carry out chemical reactions in the most efficient, economical, and environmentally responsible manner and thus reduce raw material usage, energy requirements and greenhouse gas emissions. Optimization of manufacturing steps can reduce batch-to-batch variability and has the potential to reduce metal loads in catalysts, thus reducing production costs. In chemical and petrochemical plants, catalysts manufactured with high quality can reduce feedstock requirements and energy use through improved reaction yields and selectivities. Improved reaction yields allows for smaller reactor vessels, lower temperatures of operation and more efficient use of reactants. Higher selectivities reduce the need for expensive and energy-intensive separation steps. Although the development and preparation of catalysts have been investigated for many years, numerous aspects of the various catalyst manufacturing steps are still not fully understood, and in industry the design and scale-up of catalyst manufacturing steps are often done by trial and error.

Manufacturing of Industrial Catalysts
Industrial catalyst manufacturing involves several process steps such as preparation and mixing of solutions or suspensions, crystallization, filtration, washing, mixing and kneading of powders, shaping drying, impregnation and calcination.
Before any of the preparation process starts, an active metal phase and a support need to be carefully chosen. The active metal component must be well-dispersed in order to have a large surface area when contacted with a support. On the other hand, the support has to be made of a porous and heat-resisting material. Some common processing steps in catalyst manufacturing are discussed below.
Impregnation
During this process, a solution containing active metal components (i.e. precursors) is added to the porous catalyst supports. Capillary action draws the solution into the pores and metal precursors are adsorbed onto the high surface area support. This is the first time that the metal precursor contacts the solid supports. If the volume of the solution is less than the pore volume of the support, the process is also known as incipient wetness impregnation or dry impregnation. Dry impregnation is commonly conducted in a rotating vessel, while the metal solution is sprayed on the support particle. This technique has been used widely and is still considered the favorite by the industry due to its simplicity from a practical point of view. Many types of granular mixers can be potentially used in the dry impregnation process including double cone blenders, v-blenders, and rotating drum mixers. The spraying rate, the rotation speed and the nozzle position have significant effects on the solution distribution. Other parameters that need to be considered are the concentration of the solution, the pore volume of the support, and the type and concentration of absorbing sites at the surface. Uniformity of catalyst products is one of the major concerns in this process. One wants similar metal loading to be obtained in each catalyst particle/pellet after the impregnation step.
Drying
Materials go through the process of drying after impregnation to eliminate solvents from the support. If the drying rate is slow metal salts will diffuse deeply in the pores of the support, and if the drying rate is high, precipitation will occur on the outer surface of the support. With respect to the distribution of the active component in the support, four main categories of metal profiles can be distinguished: uniform, egg-yolk, egg-shell and egg-white. The choice of the desired metal profile is determined by the required activity and selectivity and can be tailored for specific reactions and/or processes. Experimental work has shown that the metal distribution within the support is mainly determined by the impregnation and drying steps. Some factors that influence the drying process are: rate of heating, degree of liquid saturation, liquid viscosity, volume of pores and distribution of pore sizes.
Calcination
Calcination is a further heat-treatment beyond drying. In the calcination step, gas-solid and solid-solid surface reactions take place. Calcination will decompose the metal precursor with formation of an oxide and remove gaseous products and the cations or the anions which have been previously introduced. During calcination, a sintering of the precursor or of the formed oxide and a reaction of the metal oxide with the support can occur. In the case of alumina as the support, if calcination is performed at temperatures around 500-600ºC, divalent metal oxides can react with alumina on the surface of the support, forming metal aluminates which are more stable than the oxides. Oxidation reduces the size of the metal particles, which greatly affects the metal dispersion (size and shape of the metal particles on the support surface) on the nano-scale level. Careful control of temperature is required for calcination of catalysts.
Filtration
Filtration is one of the solid-liquid separation processes that are widely used in catalyst production for precipitated or crystallized catalyst particles. In cake filtration, pressure driven or vacuum-driven flow of the particulate suspension through a filter membrane or filter cloth causes the separation, and a filter cake formed from the solid particles builds up over time on the filter membrane or filter cloth. In general, the filter medium (membrane or cloth) has fairly large openings and the more stringent filtration is exerted by the cake itself, which is a porous medium where the pores are the gaps between particles. Usually, subsequent washing of the filter cake is performed in order to eliminate residual electrolytes.
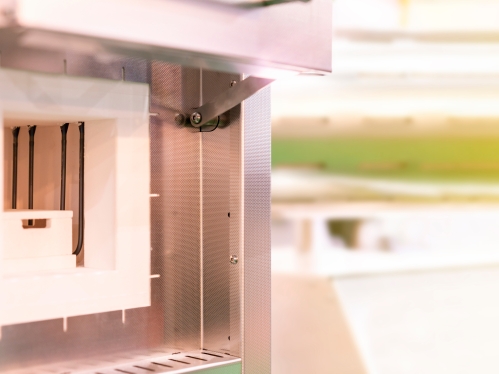
Goals
The Catalyst Manufacturing Center has been in operation for over 15 years. Our mission is to promote innovative research in the manufacturing of catalysts, and to educate a new generation of researchers in theoretical tools and engineering applications. The specific goals of the center are:
- To build and sustain a Center of Excellence in catalyst manufacturing research
- To enhance fundamental understanding of catalyst manufacturing operations
- To develop new technology for efficient catalyst manufacturing
- To provide a research, development, and education resource for industry
By combining the substantial level of expertise in particle technology, optimization, multi-scale simulation, catalysis and molecular modeling available at Rutgers, we are developing and promoting science-based methods for designing and optimizing catalyst manufacturing methods and processes such as impregnation, drying, calcination, filtration, etc. This is integrated with a number of educational activities including research training of undergraduate students, graduate students and postdoctoral fellows in the area of catalyst manufacturing. A combination of experiments and computer models has been used to improve the understanding and performance of the unit operations used to make catalysts. This knowledge, and the resulting methods and practices, have been transferred to the industrial partners to help transform this important segment of the global economy into a science-driven enterprise.
For a brochure and more information on the Catalyst Manufacturing Center please click here>>
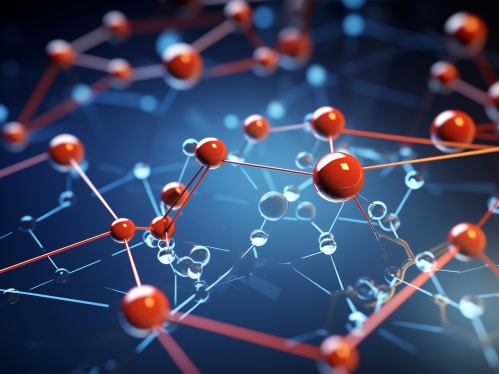


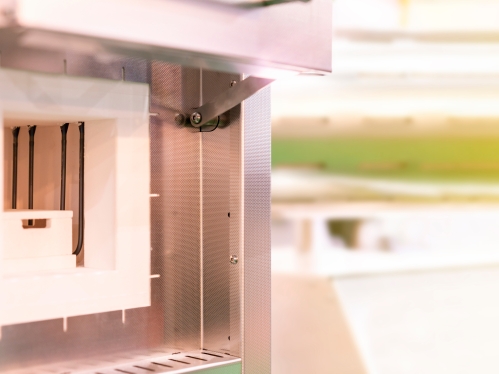
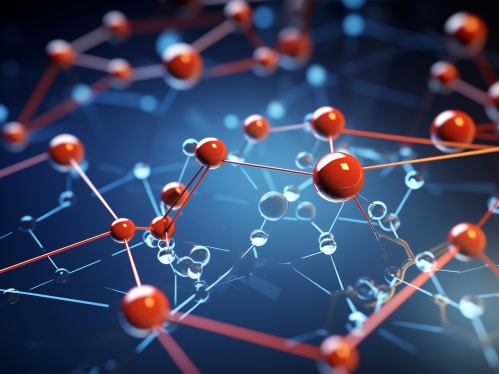
Catalyst Manufacturing Center Members
Companies
Current membership consists of companies of various sizes that develop and manufacture catalysts.
Academic Members
Benjamin Glasser, Director
William Borghard
Fernando Muzzio
Silvina Tomassone
Alberto Cuitino
The Catalyst Manufacturing Center would like to acknowledge the support and contributions of Dr. Art Chester. Art helped establish the Catalyst Manufacturing Center and was a Visiting Professor at Rutgers for many years. Art passed away in 2015 after a long illness. He was a wonderful mentor to many faculty, postdocs and students at Rutgers and we greatly benefited from his wisdom.
For more information please contact:
Professor Benjamin Glasser
Director, Catalyst Manufacturing Consortium
Chemical and Biochemical Engineering
Rutgers University
98 Brett Road
Piscataway NJ 08854, USA
Email: bglasser@rutgers.edu